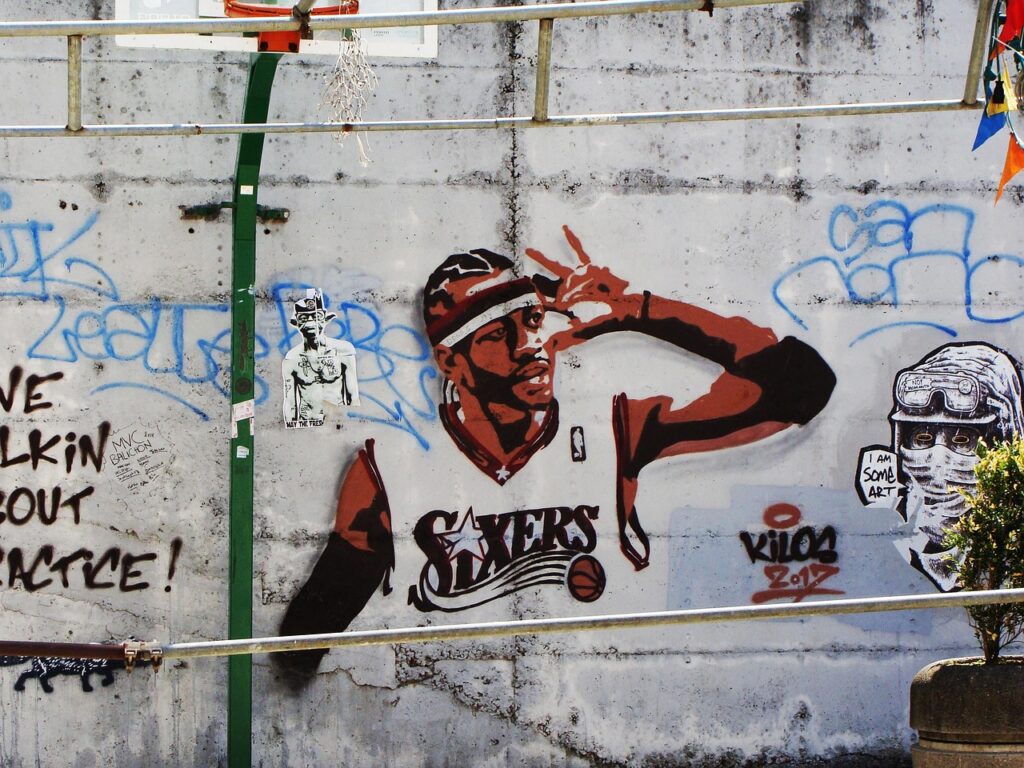
In the global market of sports – themed apparel, NBA – printed T – shirts hold significant popularity among fans worldwide. China has established itself as a major manufacturing hub for such products, offering a wide range of customization options, high – quality production, and competitive pricing. Importing NBA – printed T – shirts from China involves a series of steps, each accompanied by specific service items and associated costs. This comprehensive guide will walk you through the entire import process.
Contact us now
we are a licensed and trusted international trading company with years of experience in sourcing and fulfilling orders in China. Whether you’re looking for bulk purchases, customized products, or tailored logistics solutions, our team is dedicated to delivering transparent, reliable service.
📱 Contact Us on WhatsApp
Finding a Reputable Supplier
Service Description
The initial and crucial step in importing NBA – printed T – shirts is to identify a reliable supplier in China. There are multiple ways to source suppliers. Online B2B platforms like Alibaba, Made – in – China, and Global Sources are rich resources. These platforms list numerous manufacturers specializing in apparel production, including those with expertise in creating NBA – themed T – shirts. They provide detailed information about the suppliers, such as their product portfolios, production capacities, and customer reviews. Another effective method is to participate in international trade fairs, both in China and abroad. For example, the China International Clothing & Accessories Fair in Shanghai showcases a vast array of Chinese clothing manufacturers. Industry referrals from other businesses or contacts in the sports apparel industry can also be highly valuable. When evaluating suppliers, factors such as their experience in producing licensed sports apparel, their understanding of NBA brand requirements, production capabilities (including the number of T – shirts they can produce per day or month), and their track record in meeting quality and delivery deadlines should be carefully considered.
Cost
The cost associated with finding a supplier mainly lies in the time and resources invested in research. Some B2B platforms offer premium memberships. These memberships, which can range from \(100 to \)1000 per year depending on the platform and the level of service, provide benefits like priority placement of inquiries, access to exclusive supplier lists, and advanced search filters. Attending trade fairs can be more costly. The expenses for travel, accommodation, and exhibition participation can quickly add up. For a small – to – medium – sized business representative attending a major trade fair in China, the total cost, including airfare, hotel for a few days, and booth rental (if applicable), can range from \(3000 to \)8000. Although these costs are not directly related to the production of a single batch of T – shirts, they are an investment in establishing long – term business relationships.
Design and Licensing
Service Description
Design plays a pivotal role in the production of NBA – printed T – shirts. The client (importer) needs to collaborate closely with the supplier’s design team. The design process begins with the client providing clear ideas about the NBA – related elements they want on the T – shirts. This could include specific team logos, player images, iconic NBA moments, or unique color schemes associated with the league. The design team then creates digital mock – ups using graphic design software. These mock – ups are presented to the client for review and feedback. Multiple rounds of revisions are often necessary to ensure the final design aligns perfectly with the client’s vision.
In addition to design, obtaining the proper licensing is essential. Since NBA – themed products are protected by intellectual property rights, importers must ensure that their suppliers have the legal authorization to produce and sell NBA – printed T – shirts. This involves verifying the supplier’s licensing agreements with the NBA or its authorized licensing agents. The supplier should be able to provide documentation proving their compliance with licensing requirements.
Cost
The cost of design services varies. If the supplier offers in – house design, they may charge a flat fee or an hourly rate. For a basic design with a simple NBA logo placement, the flat fee could be around \(50 – \)200. However, for more intricate designs that incorporate detailed player illustrations or complex graphic elements, the cost can escalate to \(500 – \)1000. If an independent graphic designer is hired, the cost can be significantly higher. Freelance designers may charge anywhere from \(30 – \)150 per hour, and for a comprehensive design project for a line of NBA – themed T – shirts, the total design cost could range from \(1000 to \)5000, depending on the complexity and the number of design concepts required.
The cost of licensing is another significant aspect. Licensing fees are typically negotiated between the supplier and the NBA or its licensing agents. These fees can vary widely based on factors such as the scope of the license (e.g., whether it’s for a specific team, a limited edition collection, or the entire NBA brand), the production volume, and the duration of the license. In some cases, licensing fees can be a percentage of the total sales revenue from the NBA – printed T – shirts, usually ranging from 5% to 15%. For example, if a supplier anticipates selling \(100,000 worth of NBA – printed T – shirts in a year and the licensing fee is 10%, the annual licensing cost would be \)10,000.
Sampling and Quality Assurance
Service Description
Once the design is finalized and licensing is in place, the supplier will produce sample T – shirts. Sampling is a crucial step as it allows the importer to physically assess the product. The samples should be made using the same materials, printing techniques, and production processes that will be used for the mass production. The importer can then check for various aspects such as the quality of the fabric (e.g., its softness, durability, and colorfastness), the accuracy of the NBA logo and design printing (including color matching and print clarity), and the overall fit of the T – shirt.
The supplier will ship the samples to the importer, usually via express courier services. The importer reviews the samples and provides feedback. If there are any issues, such as fabric defects, misaligned prints, or sizing problems, the supplier will make the necessary adjustments and produce new samples. This process may require several iterations until the importer is completely satisfied with the sample quality.
Cost
The cost of sample production includes the cost of materials and labor. For a set of 3 – 5 sample T – shirts, the fabric cost can be around \(10 – \)30, depending on the type of fabric used (e.g., cotton, polyester, or a blend). The labor cost for sample production, which includes cutting, sewing, and printing, can be around \(20 – \)50. The cost of shipping the samples, especially via express courier services like DHL or FedEx, can range from \(30 – \)100, depending on the destination country and the weight of the package. So, in total, the cost of sample production and shipping can be around \(60 – \)180 for a small set of samples.
Mass Production
Service Description
After the samples are approved, the supplier proceeds with mass production. The production process for NBA – printed T – shirts involves several steps. First, the fabric is sourced. High – quality fabric is essential to ensure the comfort and durability of the T – shirts. The fabric is then cut into the appropriate sizes according to the design specifications. Next, the NBA – related designs are printed onto the fabric using techniques such as screen printing, heat transfer printing, or digital printing, depending on the complexity of the design and the desired quality. After printing, the T – shirts are sewn together, with attention paid to details such as seam strength and finishing.
The supplier is responsible for managing the entire production line, from raw material procurement to in – process quality control checks. They need to ensure that the production meets the agreed – upon quantity and quality standards. Regular inspections are carried out during production to identify and rectify any potential issues promptly.
Cost
The cost of mass production is influenced by multiple factors, including the quantity ordered, the type of fabric used, and the complexity of the printing. For a basic cotton T – shirt with a simple NBA logo print, if ordering 1000 units, the cost per unit can range from \(3 – \)8. If a more premium fabric, such as organic cotton or a high – performance blend, is used, the cost per unit may increase to \(5 – \)12. For T – shirts with more complex prints, such as multi – color designs or detailed player portraits, the cost per unit can be \(8 – \)15. The cost per unit generally decreases as the order quantity increases due to economies of scale. For example, if ordering 10,000 units, the cost per unit for a basic cotton T – shirt with a simple print could drop to \(2 – \)6.
Packaging and Labeling
Service Description
Proper packaging and labeling are essential for NBA – printed T – shirts. The packaging service includes designing and producing suitable packaging materials. This can range from simple poly – bags for individual T – shirts to more elaborate cardboard boxes or hangtags for sets or higher – end products. The packaging should not only protect the T – shirts during transportation but also enhance their visual appeal.
Labeling is equally important. Labels should include information such as the NBA logo, the name of the team or player featured on the T – shirt, the product description, size information, care instructions, and any relevant copyright or disclaimer information. The packaging and labeling design need to be in line with the overall brand image and comply with any import regulations regarding product information and safety warnings in the destination country.
Cost
The cost of packaging depends on the type and quality of the materials used. A simple poly – bag for a single T – shirt may cost as little as \(0.05 – \)0.1 per unit. A cardboard box for a set of 5 – 10 T – shirts could cost around \(0.5 – \)2 per box. If custom – designed hangtags or more elaborate packaging is required, the cost can be significantly higher, ranging from \(0.2 – \)1 per unit. The cost of label design and printing is also variable. For a basic label with simple text and a logo, the design cost may be around \(100 – \)200, and the printing cost per label can be as low as \(0.01 – \)0.05 for large – quantity orders.
Quality Control and Inspection
Service Description
Quality control is a critical part of the import process. The supplier should conduct regular in – house quality control checks during mass production. This includes inspecting the fabric for any defects, ensuring the accuracy of the printing, and checking the stitching and overall construction of the T – shirts. The importer may also choose to hire a third – party inspection company in China to conduct an independent inspection before the products are shipped.
These third – party inspection companies will randomly sample a certain percentage of the production batch, typically around 5% – 10%. They will then conduct a detailed inspection, which may include physical tests such as fabric strength testing, colorfastness testing, and checking for any potential safety hazards. After the inspection, they will provide a comprehensive inspection report to the importer, highlighting any issues found and recommending solutions.
Cost
The cost of in – house quality control by the supplier is usually factored into the production cost. However, if the importer hires a third – party inspection company, the cost will be additional. Third – party inspection companies typically charge based on the size of the production batch and the complexity of the inspection. For a batch of 1000 – 5000 T – shirts, the inspection fee can range from \(300 to \)1000. The fee may increase if more in – depth testing is required, such as specialized fabric analysis or compliance with specific international standards.
Shipping and Logistics
Service Description
Once the production is complete and the products have passed quality control, they need to be shipped to the importer’s destination. Shipping services include arranging for transportation, whether by air, sea, or land. For international shipments, the supplier will handle the necessary customs documentation, such as commercial invoices, packing lists, and certificates of origin. They may also work with freight forwarders to ensure smooth transportation.
Air freight is a faster option but more expensive, suitable for smaller and more urgent orders. Sea freight is more cost – effective for larger shipments but takes longer. In some cases, if the destination is within China or in a neighboring country, land transportation may be considered. The supplier will also be responsible for ensuring that the T – shirts are properly packed and protected during transit to prevent any damage.
Cost
The cost of shipping depends on the shipping method, the weight and volume of the shipment, and the destination. Air freight costs for a small – scale shipment of, say, 100 kilograms of NBA – printed T – shirts from China to a destination in Europe or North America can range from \(500 to \)1200. Sea freight for a 20 – foot container, which can hold a large quantity of T – shirts, can cost from \(1000 to \)3000 from China to major ports in Europe or North America. In addition to the freight cost, there may be customs clearance fees, which can range from \(100 to \)500 depending on the value of the goods and the complexity of the customs process. If a freight forwarder is used, their service fee can be around \(200 – \)1000, depending on the scope of services provided.
Overall Cost Estimation
For a small – scale order of, say, 500 NBA – printed T – shirts:
- Finding a supplier: Assuming using a B2B platform with a mid – range membership, around $300.
- Design and licensing: If using the supplier’s in – house design for a moderately complex design and a licensing fee of 8% of the expected sales revenue (assuming an average selling price of \(20 per T – shirt, so expected revenue of \)10,000 and a licensing fee of \(800), and a design cost of \)300, the total for this category is $1100.
- Sampling and quality assurance: Around $100 for sample production and shipping.
- Mass production: For basic cotton T – shirts at \(5 per unit, the production cost would be \)5 x 500 = $2500.
- Packaging and labeling: Assuming simple packaging and basic labels, around \(200 for packaging materials and \)100 for label design and printing.
- Quality control and inspection: If hiring a third – party inspector, around $500.
- Shipping and logistics: Assuming air freight for a small – scale shipment, around $600.
In total, for such a small – scale order, the cost can be around $5300. For large – scale commercial orders, such as ordering 10,000 units, the costs will be influenced by economies of scale. The production cost per unit will decrease, but the overall cost of shipping and logistics may increase due to the larger volume. However, the total cost per unit will generally be lower compared to small – scale orders.
[Labels: Importing NBA – printed T – shirts, China – made sports apparel import, T – shirt import process, Import service cost for apparel, Licensed sports merchandise import]